NASA Readies Moon Rocket for the Future with Manufacturing Innovation
NASA’s Artemis campaign will send astronauts, payloads, and science experiments into deep space on NASA’s SLS (Space Launch System) super heavy-lift Moon rocket. Starting with Artemis IV, the Orion spacecraft and its astronauts will be joined by other payloads atop an upgraded version of the SLS, called Block 1B. SLS Block 1B will deliver initial elements of a lunar space station designed to enable long term exploration of the lunar surface and pave the way for future journeys to Mars. To fly these advanced payloads, engineers at NASA’s Marshall Space Flight Center in Huntsville, Alabama, are building a cone-shaped adapter that is key to SLS Block 1B.

The payload adapter, nestled within the universal stage adapter sitting atop the SLS Block 1B’s exploration upper stage, acts as a connecting point to secure a large payload that is co-manifested – or flying along with – the Orion spacecraft. The adapter consists of eight composite panels with an aluminum honeycomb core and two aluminum rings.
Beginning with the Artemis IV mission, SLS Block 1B will feature a new, more powerful upper stage that provides a substantial increase in payload mass, volume, and energy over the first variant of the rocket that is launching Artemis missions I through III. SLS Block 1B can send 84,000 pounds of payload – including both a crewed Orion spacecraft and a 10-metric ton (22,046 lbs.) co-manifested payload riding in a separate cargo compartment – to the Moon in a single launch.
Artemis IV’s co-manifested payload will be the Lunar I-Hab, one of the initial elements of the Gateway lunar space station. Built by ESA (European Space Agency), the Lunar I-Hab provides expanded capability for astronauts to live, work, conduct science experiments, and prepare for their missions to the lunar surface.
Before the Artemis IV mission structure was finalized, NASA engineers needed to design and test the new payload adapter.
“With SLS, there’s an intent to have as much commonality between flights as possible,” says Brent Gaddes, Lead for the Orion Stage Adapter and Payload Adapter in the SLS Spacecraft/Payload Integration & Evolution Office at NASA Marshall.
However, with those payloads changing typically every flight, the connecting payload adapter must change as well.
“We knew there needed to be a lot of flexibility to the payload adapter, and that we needed to be able to respond quickly in-house once the payloads were finalized,” says Gaddes.
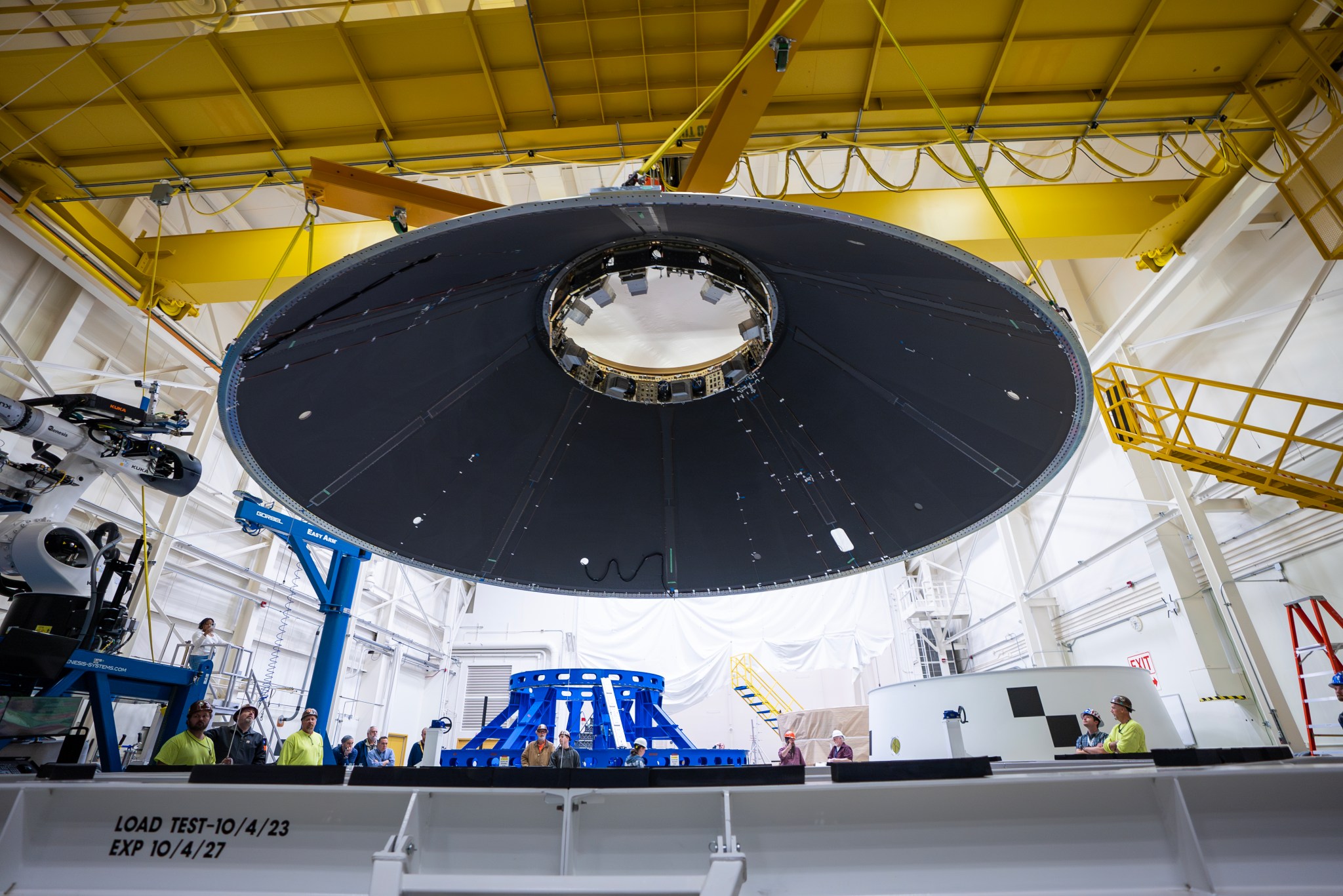
A Flexible Approach
The required flexibility was not going to be satisfied with a one-size-fits-all approach, according to Gaddes.
Since different size payload adapters could be needed, Marshall is using a flexible approach to assemble the payload adapter that eliminates the need for heavy and expensive tooling used to hold the parts in place during assembly. A computer model of each completed part is created using a process called structured light scanning. The computer model provides the precise locations where holes need to be drilled to hold the parts together so that the completed payload adapter will be exactly the right size.
“Structured light has helped us reduce costs and increase flexibility on the payload adapter and allows us to pivot,” says Gaddes. “If the call came down to build a cargo version of SLS to launch 40 metric tons, for example, we can use our same tooling with the structured light approach to adapt to different sizes, whether that’s for an adapter with a larger diameter that’s shorter, or one with a smaller diameter that’s longer. It’s faster and cheaper.”
NASA Marshall engineers use an automated placement robot to manufacture eight lightweight composite panels from a graphite epoxy material. The robot performs fast, accurate lamination following preprogrammed paths, its high speed and precision resulting in lower cost and significantly faster production than other manufacturing methods.
At NASA Marshall, an engineering development unit of the payload has been successfully tested which demonstrated that it can handle up to three times the expected load. Another test version currently in development, called the qualification unit, will also be tested to NASA standards for composite structures to ensure that the flight unit will perform as expected.
“The payload adapter is shaped like a cone, and historically, most of the development work on structures like this has been on cylinders, so that’s one of the many reasons why testing it is so important,” says Gaddes. “NASA will test as high a load as possible to learn what produces structural failure. Any information we learn here will feed directly into the body of information NASA has pulled together over the years on how to analyze structures like this, and of course that’s something that’s shared with industry as well. It’s a win for everybody.”
With Artemis, NASA will explore more of the Moon than ever before, learn how to live and work away from home, and prepare for future human exploration of the Red Planet. NASA’s SLS (Space Launch System) rocket, exploration ground systems, and Orion spacecraft, along with the human landing system, next-generation spacesuits, Gateway lunar space station, and future rovers are NASA’s foundation for deep space exploration.
News Media Contact
Jonathan Deal
Marshall Space Flight Center, Huntsville, Ala.
256-544-0034
jonathan.e.deal@nasa.gov