NASA’s Curiosity Rover May Have Solved Mars’ Missing Carbonate Mystery
3 min read
Preparations for Next Moonwalk Simulations Underway (and Underwater)
New findings from NASA’s Curiosity Mars rover could provide an answer to the mystery of what happened to the planet’s ancient atmosphere and how Mars has evolved over time.
Researchers have long believed that Mars once had a thick, carbon dioxide-rich atmosphere and liquid water on the planet’s surface. That carbon dioxide and water should have reacted with Martian rocks to create carbonate minerals. Until now, though, rover missions and near-infrared spectroscopy analysis from Mars-orbiting satellites haven’t found the amounts of carbonate on the planet’s surface predicted by this theory.
Reported in an April paper in Science, data from three of Curiosity’s drill sites revealed the presence of siderite, an iron carbonate mineral, within the sulfate-rich rocky layers of Mount Sharp in Mars’ Gale Crater.
“The discovery of abundant siderite in Gale Crater represents both a surprising and important breakthrough in our understanding of the geologic and atmospheric evolution of Mars,” said Benjamin Tutolo, associate professor at the University of Calgary, Canada, and lead author of the paper.
To study the Red Planet’s chemical and mineral makeup, Curiosity drills three to four centimeters down into the subsurface, then drops the powdered rock samples into its CheMin instrument. The instrument, led by NASA’s Ames Research Center in California’s Silicon Valley, uses X-ray diffraction to analyze rocks and soil. CheMin’s data was processed and analyzed by scientists at the Astromaterials Research and Exploration Science (ARES) Division at NASA’s Johnson Space Center in Houston.
“Drilling through the layered Martian surface is like going through a history book,” said Thomas Bristow, research scientist at NASA Ames and coauthor of the paper. “Just a few centimeters down gives us a good idea of the minerals that formed at or close to the surface around 3.5 billion years ago.”
The discovery of this carbonate mineral in rocks beneath the surface suggests that carbonate may be masked by other minerals in near-infrared satellite analysis. If other sulfate-rich layers across Mars also contain carbonates, the amount of stored carbon dioxide would be a fraction of that needed in the ancient atmosphere to create conditions warm enough to support liquid water. The rest could be hidden in other deposits or have been lost to space over time.
In the future, missions or analyses of other sulfate-rich areas on Mars could confirm these findings and help us better understand the planet’s early history and how it transformed as its atmosphere was lost.
Curiosity, part of NASA’s Mars Exploration Program (MEP) portfolio, was built by NASA’s Jet Propulsion Laboratory, which is managed by Caltech in Pasadena, California. JPL leads the mission on behalf of NASA’s Science Mission Directorate in Washington.
For more information on Curiosity, visit:
https://science.nasa.gov/mission/msl-curiosity
News Media Contacts
Karen Fox / Molly Wasser
NASA Headquarters, Washington
202-358-1600
karen.c.fox@nasa.gov / molly.l.wasser@nasa.gov
Andrew Good
Jet Propulsion Laboratory, Pasadena, Calif.
818-393-2433
andrew.c.good@jpl.nasa.gov
Details
Explore More
Discover Related Topics
Curiosity Rover (MSL)
/Curiosity%20Rover%20(MSL)%20(Clean).png)
Ames Research Center
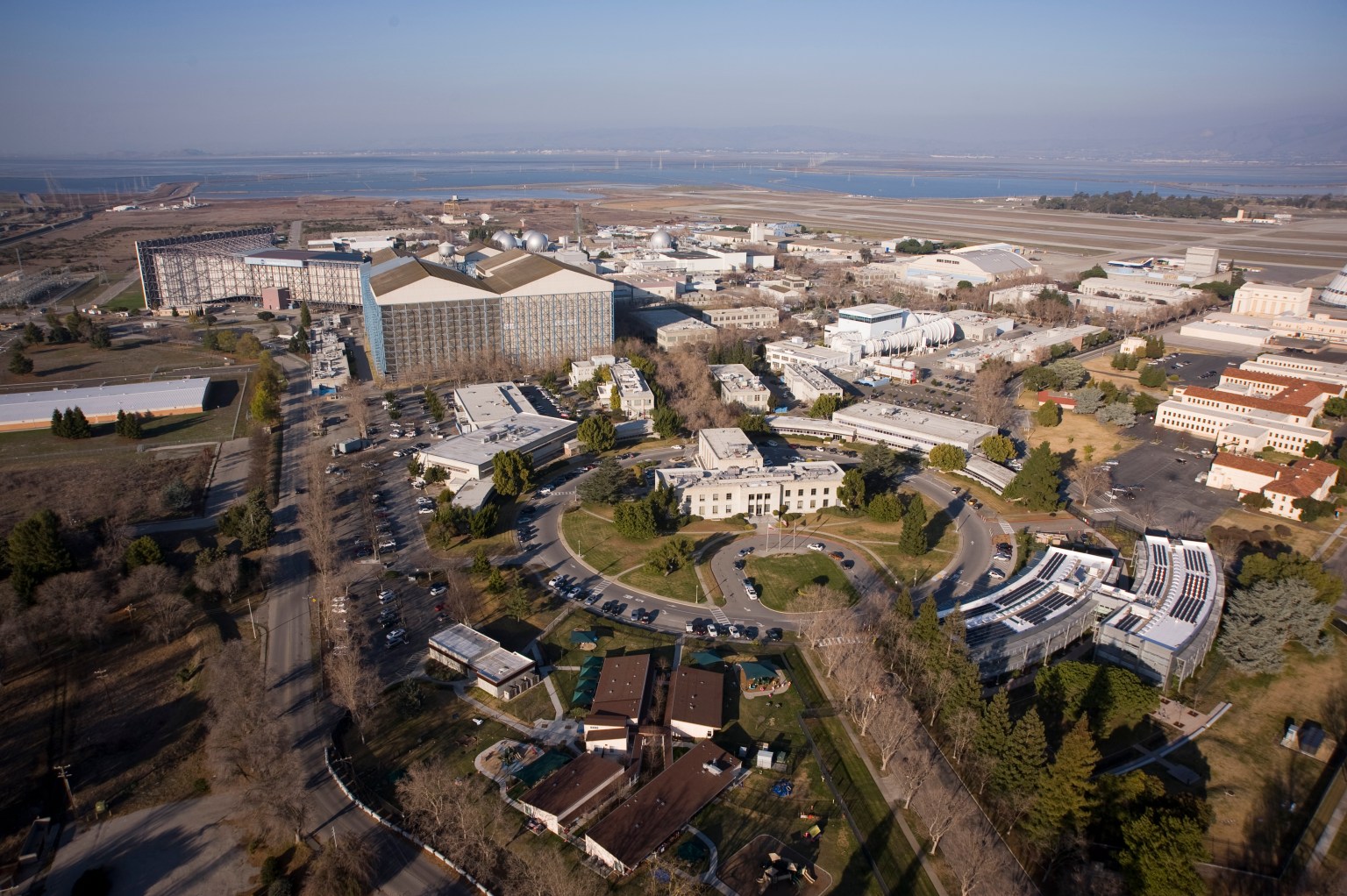
Mars
Mars is the fourth planet from the Sun, and the seventh largest. It’s the only planet we know of inhabited…
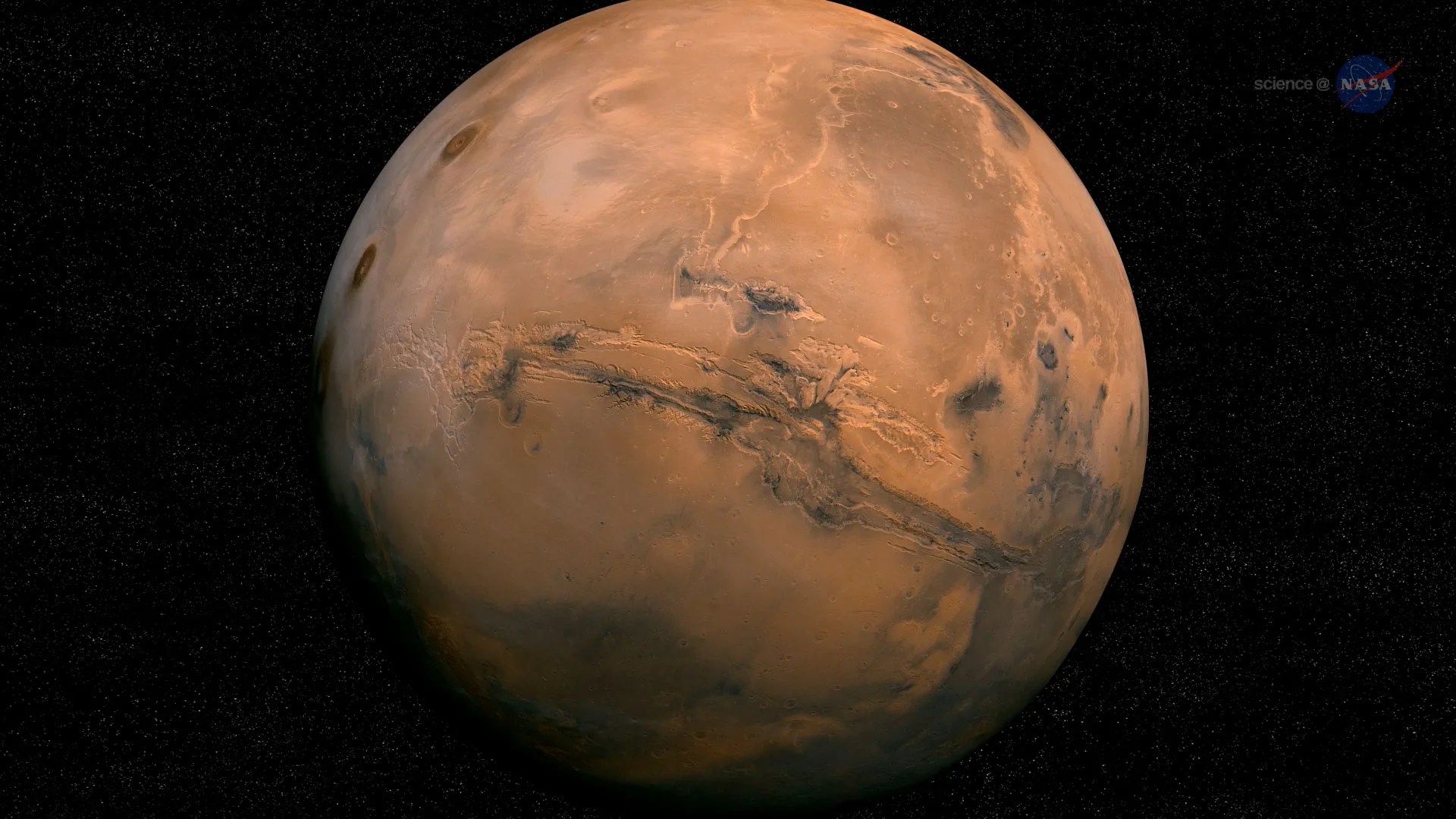
Curiosity Science Instruments
Curiosity’s scientific instruments are the tools that bring us stunning images of Mars and ground-breaking discoveries.
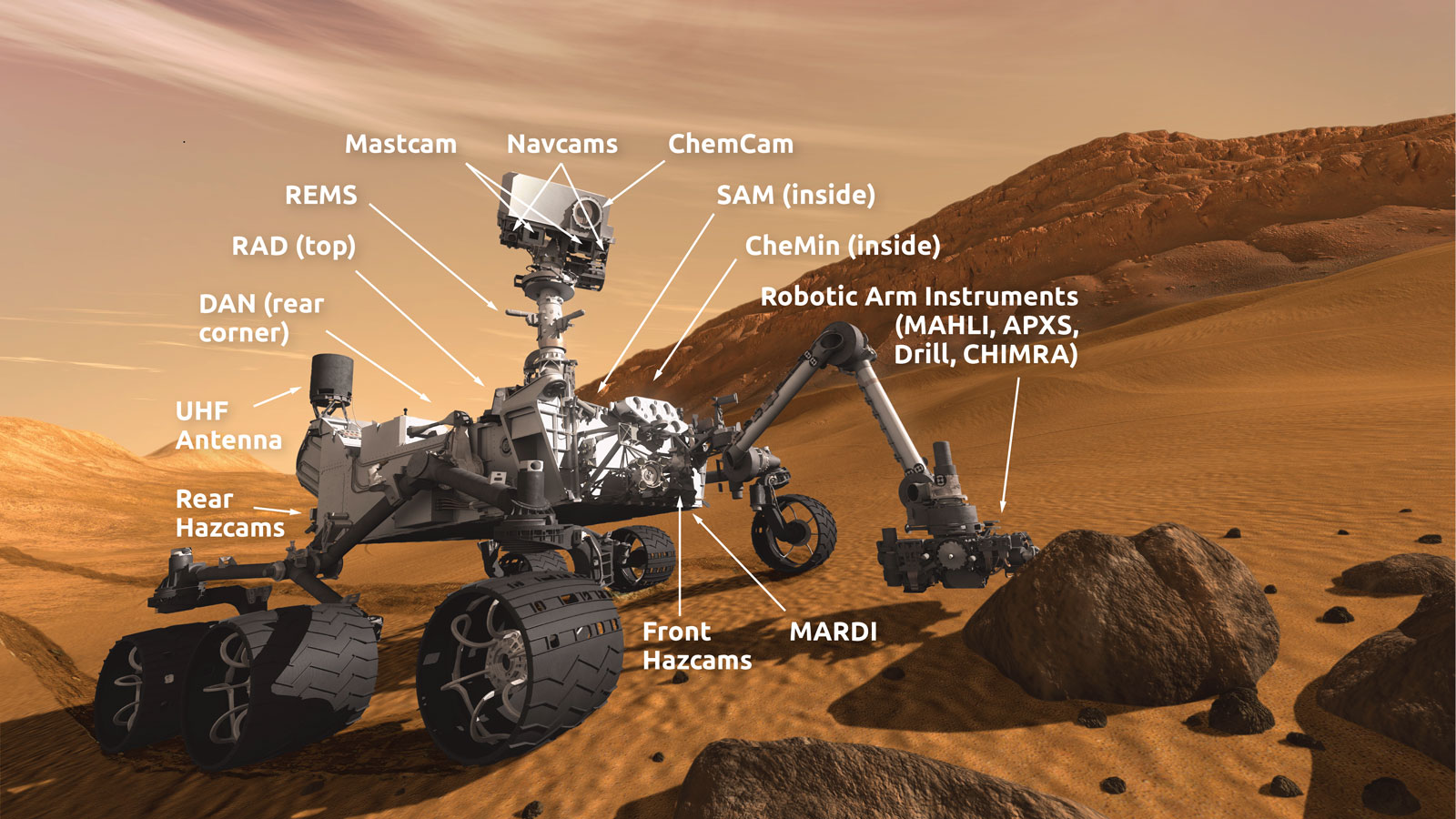